Mahendra Singhi has some interesting stories to tell about what could be a very boring subject: cement. About how he met Nobel-winning climate guru Al Gore during a hastily planned trip to Washington in 1999. That’s where he first learnt about carbon credits or a mechanism that allows companies to buy carbon offsets from outside projects which avoid greenhouse gas emissions. It was his first tryst with the concept of sustainability or the idea of being clean, green, and still profitable. He was so sold on the idea that it became his business mantra after that. In the next three years, the company he headed at the time, Shree Cement, would make ₹45 crore by cleaning up its cement manufacturing process to earn carbon credits.
It’s a hot June day in Delhi with temperatures at a high 48 degrees Celsius. I am sitting with Singhi, who now heads Dalmia Cement,in an air-conditioned office in central Delhi. He tells me there was a time in the 1970s and 1980s when if he saw smoke billowing from a factory chimney, he’d be content seeing the plant was in full production. “At the time people didn’t realise we were not emitting dust,but we were emitting money,” the 66-year-old Singhi tells Fortune India. He says that attitude is changing now. “We want to work for profitability and sustainability... We came up with the philosophy of use less, produce more. You use a lesser quantum of the right mate-rial but try to use more waste material from others,” he says. The company says it has reduced the use of limestone in cement and is using waste material from industries like steel instead.
Dalmia Cement is part of a growing club in India Inc that is cleaning up its act as consciousness about the dangers of climate change and environmental degradation grows across the world. From offices cutting down on plastic cups and printing paper to factories controlling the effluents released into water bodies, the air, and landfills, companies are making sustainability a part of their everyday business vocabulary and process. As part of their efforts to save the environment, companies in sectors ranging from automobiles and metals to cement and FMCG are making big changes such as cutting down water consumption, using clean renewable fuels such as solar and wind, recycling waste material, and incorporating sustainable practices into the manufacturing process.
The U.S. Environment Protection Agency defines sustainable manufacturing as the creation of manufactured products through economically-sound processes that minimise negative environmental impacts while conserving energy and natural resources. “Business as usual is no longer good enough in the sense that the environment considerations have become paramount. Because of climate change, climate action is very crucial, and corporations need to make a contribution,” says Anirban Ghosh, chief sustainability officer at Mahindra Group.
It’s been a long time coming but companies don’t have a choice but to walk on the path of sustainability. Though the scale is still tiny, heavy fines by government agencies on polluters, stricter emission norms to comply with the Paris Climate Agreement, and the fear of depleting resources are making Indian companies look beyond their bottom lines to adopt green practices to protect the environment. India is the world’s third largest emitter of carbon dioxide—one of the main culprits for environmental damage and climate change—after China and the U.S. Although it resisted targets on green-house gas emissions for years, it finally agreed to reduce its carbon emission intensity by 33-35% from 2005 levels by 2030 at the historic Paris climate change conference as its air and water quality deteriorated dramatically. Sewage and industrial waste are being dumped into rivers and water bodies, groundwater is highly contaminated, waste management is poor, and growing landfills are affecting the environment and health. According to the World Economic Forum, seven of the world’s 10 most polluted cities are in India. The effect of global warming is most apparent in India today as it grapples with an unprecedented water crisis.
While the energy sector is one of the biggest emitters of carbon dioxide, most big industries in general add significantly to pollution and the depletion of natural resources. In India, industries neglected the environment for years because fines on polluters were low, but now that the government is cracking down many of them are going green. “One of the major disruptions has been the setting up of the National Green Tribunal (NGT) in 2010,” says Nawneet Vibhaw, partner at law firm Khaitan & Co, who specialises in environmental dispute resolution. “The NGT has definitely created fear in the minds of the violators and thanks to the NGT, many Indian companies including smaller businesses, have become more compliant than what they used to be a decade earlier.”
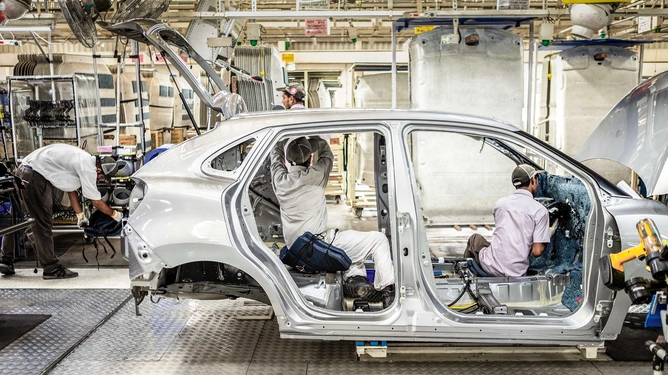
Sustainability is the buzzword everywhere from big businesses like Dalmia Cement and ITC to smaller companies like apparel cooperative Avani in Kumaon. Nearly 43% of ITC’s energy consumption is from renewable sources while Avani works with a variety of natural fibres and materials to create its artisanal products. But they are not alone. Businesses across the board are looking to reduce their carbon footprint. According to environmental disclosure campaign platform CDP, major Indian businesses such as Infosys, Dalmia Bharat, TataMotors, Hatsun Agro Products, and Mahindra Holidays have committed to using 100% renewable electricity in their global operations by joining global green electricity campaign RE100. And 25 Indian companies have committed to the Science Based Targets initiative (SBTi), which helps companies determine how quickly they need to reduce their greenhouse gas emissions. Three companies—Mahindra Sanyo Special Steel, Hindustan Zinc, and Wipro—have got their targets approved.
Let’s look at Dalmia Cement, India’s fourth-largest cement maker. Singhi says the 80-year-old cement manufacturer is working hard towards sustainability, and wants to be carbon negative by 2040. But how does one make cement, one of the most polluting materials, green and still make a profit? To be sure, even global giants from Switzerland’s Lafarge-Holcim to Brazil’s Votorantim Cimentos are finding it difficult to find buyers for their green cement, which is more expensive, according to a recent Bloomberg report.
However, Singhi is confident. The cement veteran explains the key to making green cement is reducing the quantity of limestone in it. He says the company was traditionally using 70-80% limestone in cement, but has now reduced that to 50% and replaced it with industrial slag. The process of burning limestone in 1,400-degree furnaces is the cause of most emissions in the cement industry; if the proportion of limestone is reduced,emissions go down.
Reducing the usage of natural resources is something that other industries are looking at as well. Take Maruti Suzuki, for instance. At one of the company’s largest plants in Manesar, employees follow the so-called Kaizen concept or the Japanese philosophy of “change for better”. Workers and managers are all encouraged to find ways of making products and processes more efficient and reducing costs—in other words, making them more sustainable. Take something small like cutting the size of bolts by a millimetre or using lighter steel where possible to reduce the total amount of steel used. The company says it has managed to reduce the use of resources such as steel per vehicle in a big way even with small changes such as these, considering the volumes are so large. The Manesar plant, for instance, produces one car a minute and uses 470 tonnes of steel every day. The company has also started controlling its use of substances of concern (SoC) like lead and mercury in its mass production vehicles and making its cars 95% recoverable and 85% recyclable.
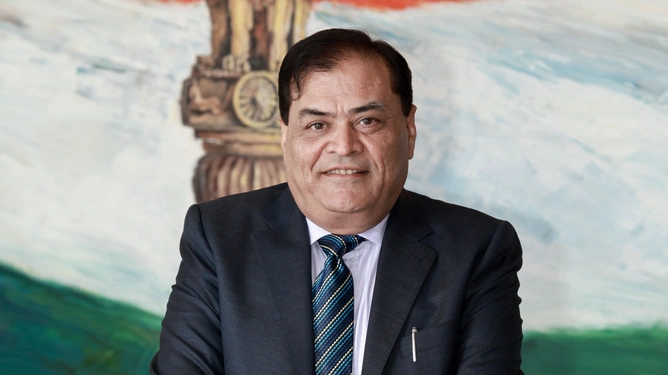
As part of its efforts to protect the environment, Maruti is also making a foray into electric vehicles and has stopped making diesel vehicles. It says the addition of CNG and Smart Hybrids helped India’s largest carmaker bring down carbon dioxide emissions by over 175,000 tonnes in 2018-19. The company says one reason is to comply with BS VI emission norms to be rolled out next year, but it also sees attitudes of consumers changing. “The purchasing power in India might be totally different from abroad but because of the Internet and TV, consumers know what is happening all across the world, youngsters are becoming very aware,” says P. Panda, executive director of engineering at Maruti Suzuki India.
Being ready for a future in which environment norms will become stricter as countries comply with their emission targets in keeping with the Paris Agreement is another factor driving the change in corporate India. Tata Steel, the country’s second-largest steelmaker, is working on a recycling steel plant in Haryana to reduce its carbon footprint. Steel is the most recycled material on the planet, but it is mostly recycled by the informal sector, the kabadiwalas or scrap dealers. Tata Steel wants to change that by formalising steel recycling in the country. The company says it has cut its coking coal usage dramatically in the past four to five years, reducing its carbon dioxide emissions. “Going forward there will be embargoes on how much you can emit. Europe is already doing that,the developed world has already begun to do that in some small ways,”says Sanjiv Paul, vice president of safety, health, and sustainability at Tata Steel. “We are certain this will catch up really fast and India will be impacted sooner rather than later.”
Companies are also collaborating with each other to reuse and recycle as they reduce emissions and still make money. Cement firms, for instance, are taking waste materials like fly ash and slag from steel makers to make their products green. Dalmia’s Singhi says they are one of the country’s biggest manufacturers of the comparatively more environment-friendly slag cement. Tata Steel is also looking for ways to use LD slag, another byproduct of the steel making process,in road building. Paul says it is in talks with government think tank NITI Aayog and the ministry of commerce to make LD slag the standard in road making. So far, it all ends up in landfills. “That is a waste of land as well as an important resource,” says Paul.
Coming back to water, industry accounts for about 5% of the country’s water usage, but it is one of the big contributors to water pollution. Companies are moving towards using less water in production and treating the effluents instead of dumping them into rivers. Mahindra’s Ghosh says 30% of the water in the conglomerate’s auto and farm businesses gets reused. Ghosh says the company has two factories that don’t use municipality water for 200 days in a year as a result of water harvesting.
India has several laws governing environmental protection. The Environment Protection Act, which sets standards for emissions by industry, regulates the location of industries; management of hazardous wastes, and protection of public health and welfare. The Air (Prevention and Control of Pollution) Act,1981, prohibits the use of polluting fuels and substances that increase air pollution. Last year, the NITI Aayog recommended the waste-water discharge into rivers be reduced to zero.
Experts believe companies have become more compliant since the establishment of the NGT. Khaitan & Co’s Vibhaw says these steps are a good start even if they are small in terms of the overall pollution caused by industry. “In the next five to 10 years, even if more than 50% of the industries are adopting international best practices like GRI standards and carbon disclosure under CDP, it will create a very good impact on all others, who may not even know about such best practices right now,” he says.
(This story was originally published in August 2019 issue of the magazine.)