TWITTER HAS for years been a frontier for breaking news. Among regulars at the microblogging site is Union minister for road transport and highways Nitin Gadkari. In October 2022, he tweeted that government has decided to defer implementation of a proposal mandating at least six airbags in passenger vehicles by one year. “Considering the global supply chain constraints being faced by the auto industry and its impact on the macroeconomic scenario, it has been decided to implement the proposal from October 1, 2023,” he said.
This came as a salve for carmakers. Society Of Indian Automobile Manufacturers (SIAM) had earlier exhorted Gadkari’s ministry to “review and reconsider” the decision as “side and curtain bags are not mandated anywhere else” in the world. “SIAM is taking up the issue with Central government, not only for six airbags but also three-point seatbelts at the back, as those are also required now. Putting six airbags without installing (rear) seat belts will not serve any useful purpose. There has to be a timeline for that as well,” R.C. Bhargava, chairman, Maruti Suzuki India (MSIL), India’s largest carmaker, told Fortune India. MSIL will be most affected by the mandate as it dominates the entry-level segment. “The focus has been on adding passive safety features to drive up the price. They, along with NCAP (New Car Assessment Programs) standards, have no significant impact on number of accidents,” he says. “There exists (in many countries) a rigorous programme for training and testing before a person gets a driving licence. There’s no such thing in India.”
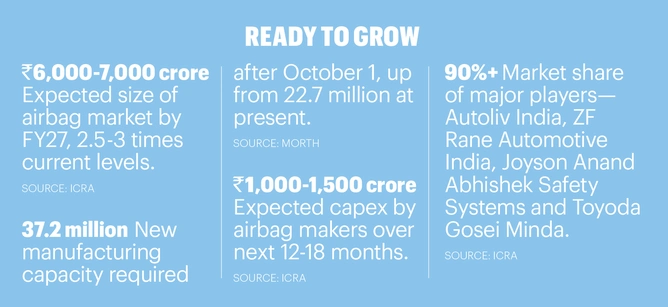
Bhargava welcomed the deferment saying government understood the industry’s concern about paucity of time for modifying chassis to accommodate the additional airbags. “When you have to put six airbags, you not only have to make adjustments in rear seat — from where airbags will start inflating — but also in side trims and doors. It is difficult to accommodate more than two people in rear seat in some small cars. So, when you install airbags that will inflate from side doors, you have to blow out the body,” says Hemant Thakkar, director, transport, logistics and mobility, CRISIL. Thakkar says this cannot be done in just eight-ten months. “First, companies will have to make changes on the drawing board. Then, they will have to see what materials or components are required to make these changes and identify who will supply those components. Then, they will need a prototype. All this has cost implications, too,” he says.
However, the industry realises that Gadkari's ministry has provided only a temporary relief. Suresh K.V., president and regional head, ZF India, which makes airbags for passenger vehicles, says government will not skip the mandate. “Its stance is clear. Life of someone travelling in an Alto, for instance, is not lesser than life of someone travelling in a Mercedes-Benz,” he says. Suresh is reiterating the point recently raised by Gadkari in Par- liament: “If a poor man dies, we let him die, and save the rich man, is it?”
“This has always been a sensitive topic. There were always some OEMs (original equipment makers) raising concerns about incremental costs and timelines,” says Suresh. “I personally believe something as critical to occupant safety should not have been deferred. However, given the global supply-chain issues the industry is facing, it seems like the prudent thing to do,” says Suresh. He believes the mandate cannot be further deferred. “Do we have a choice? Can this be deferred by two years?” he asks. Suresh cites direct transition from BS-IV to BS-VI emission norms to stress the industry’s ability to push itself to meet latest regulations even if they are stiff.
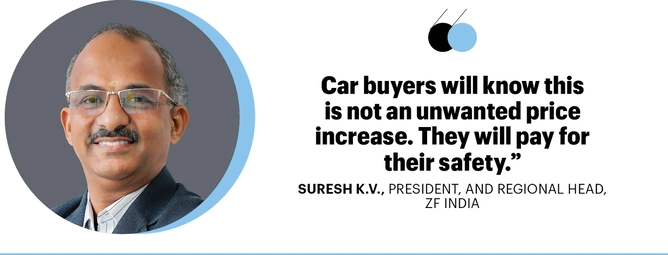
Thakkar of CRISIL says stakeholders have been ‘very, very pushy.’ “They do not want this regulation in a certain way because until FY21, demand was stiff, and any price escalation would have further suppressed it. So, from that perspective, they were pushy. But now government has said this has to happen,” he says.
The industry realises this, which is why OEMs, despite their apprehensions, are working out plans to meet the October 2023 deadline. Ancillary players, despite hurdles, are drawing up plans to tap the huge opportunity on offer.
Supply Chain, Other Constraints
Companies that make safety systems are expecting good business from airbags. But they will find it hard to source components such as semiconductors, crucial to timely deployment of airbags, due to supply-chain disruptions. Auto industry the world over is struggling to meet demand due to semiconductor shortage triggered by Covid-19 and exacerbated by Russia-Ukraine war. “We don’t see the semiconductor crisis behind us even in first half of FY24,” says Suresh of ZF India.
Automotive Components Manufacturers Association (ACMA) says only 40% of the airbag manufacturing process is indigenised and critical components, including the high-strength fabric, are imported. “Some key components of airbags such as sensors and inflators are imported and, hence, supply chain is critical for their sourcing,” says Vinutaa S., vice president and sector head, corporate ratings, ICRA. The industry imports 60-70% of its components, primarily from overseas parents/joint venture partners, according to the rating agency. ICRA says the airbag market will grow to ₹6,000-7,000 crore by FY27. That’s about 2.5-3x growth from current levels.
Sunil Bohra, group chief financial officer and group chief strategy officer, Uno Minda, says component makers have been anticipating this regulation for past few years. “All this talk has come in public discourse recently. We were expecting this for some time and planned our last expansion accordingly,” says Bohra. He says the company has headroom to further increase manufacturing. “We have incremental capacity at our new plant in Gujarat. The only thing we will need is some extra types of equipment. Some have been ordered,” he says. Ministry of road transport and highways says India’s airbag manufacturing capacity is 22.7 million. The estimated increase in production next year is 37.2 million, it says, quoting SIAM data. By all accounts, this is a huge business opportunity.
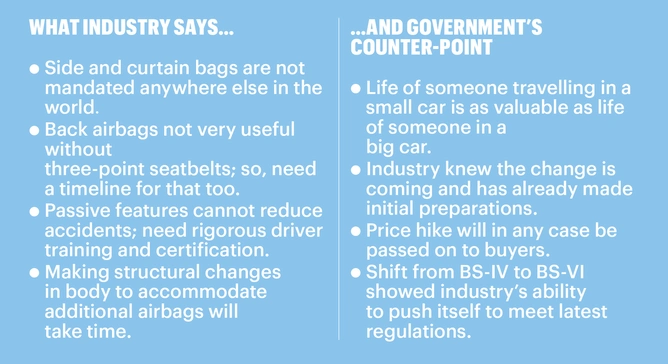
Topline Expansion
Industry observers say component companies are expected to grow at a much faster rate than the larger automobile industry due to rise in number of components per car. “The sentiment in the auto component industry is positive. The value per component increases with each new regulation. Therefore, even if volumes do not increase, value per vehicle will rise,” says Thakkar. Premiumisation will help auto component players improve realisations, he adds.
In November last year, OLX Autos and CRISIL released a report which said auto industry volumes shrunk at a CAGR of 3% between FY17 and FY21 on the back of economic slowdown and Covid-19. But growth in value was 2% per year, it said. When the industry started bouncing back, in FY22, volumes grew 13% to 31 lakh units and value grew 25% to ₹3.3 lakh crore.
This will cushion the impact of costs incurred in fitting additional airbags. “The mandatory content per vehicle for airbag manufacturers is expected to rise from ₹3,000-4,000 to ₹8,000-10,000 by October 1, 2023. Cost for OEMs could increase further depending on modifications required in structure and need for additional sensors,” says Vinutaa of ICRA.
According to Thakkar of CRISIL, OEMs’ costs will rise by ₹10,000 per airbag. “Even if you consider a basic airbag, with only polymers, springs and sensors, it will not cost less than ₹8,000. So, we are looking at an additional ₹40,000 for four airbags,” he says. However, economies of scale can bring down costs. “Prices could come down. But this also means that OEMs can hike prices by ₹30,000-40,000,” he says. Suresh of ZF India says price increase will be substantial but not drastic. He also believes that the Indian car buyer has evolved and will take the price increase in his stride. “The buyers will know this is not an avoidable increase. They will pay for safety,” says Suresh.
His sentiments are echoed by Vinnie Mehta, director general, ACMA. “There is a cost to quality but quality eventually wins. This means we need to offer vehicles that are safer for occupants and pedestrians as well as environment. Regulations may hurt in the beginning but I guess there are many ways of circumventing the price increase,” he says, adding that “as an apex body, we always appreciate when component makers look inwards, become leaner and cut unnecessary costs. But life is priceless. I don’t buy that increase in cost will adversely impact the market.” Mehta says the narrative is shifting from affordability to getting the best in quality and safety.
Growth Plans
The sharp spike in demand for airbags means there is immense scope for localisation and development of Tier-II vendor ecosystem considering that the industry imports 60-70% components. This can improve margins of component makers and ease supply-chain challenges for airbag manufacturers. Airbag component manufacturing is part of PLI Scheme for facilitating indigenous manufacturing. Most airbag makers are already in the process of making key components locally. For example, Uno Minda is through with the primary capex and is now focusing on building incremental capacity. “Capacity building in next one year is critical to meeting regulatory requirements in a timely manner. Several players have started capacity enhancements in last six-eight months to scale up facilities. ICRA expects a capex of ₹1,000-1,500 crore in next 12-18 months for capacity enhancement and localisation,” says Vinutaa. “It’s a matter of time before capacity increases,” says Suresh of ZF India. However, ICRA says that unless there is adequate backward integration for incremental airbags expected to be produced, imported content will rise.
But the industry’s growth potential is certain. Sukhdeep Sandhu, head, passive safety and sensorics, Continental Automotive India, believes the Indian automobile industry has shown its mettle in past two years, which were marred by Covid-19 pandemic and other black-swan events. Continental India makes control units of airbags. Sandhu believes the industry has been doing exceedingly well. “Had there been significant roadblocks, it would not have been doing such numbers,” he says. Continental says it is well-positioned in India as one of the market leaders. “We see higher volumes and use of production lines,” he says. Continental made more than a million control units for the Indian market last year and has been making an aggregate of one million units for past four-five years.
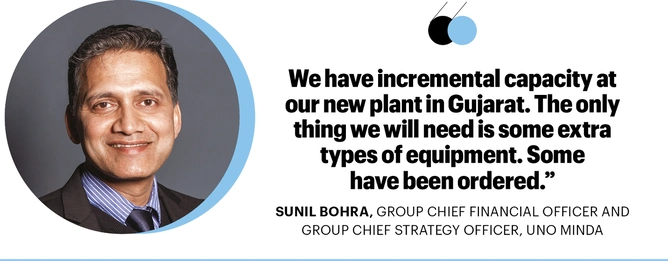
Sandhu’s sentiments are echoed by Suresh of ZF India. “There will be a lot of benefits for our JV in India when two airbags become six and we win more projects,” he says. ZF, a German maker of car parts, operates in India via a joint venture with Chennai’s Rane Group.
Such ventures are common in the auto components industry. ICRA says lack of indigenous capability and adequate volumes are behind the trend of overseas parents/joint venture partners. However, Bohra of Uno Minda says this has always been a trend. “It’s not that we cannot develop technologies. There is a timeline for product development. It takes anywhere between three and six years to incubate, develop a prototype and manufacture a product. The customer does not have the luxury of time. This is why you are seeing technical licensing, joint ventures. For us, a joint venture is like marriage; it is forever. None of our joint ventures has a sunset clause,” he says.
Bohra says the company expects airbags vertical to rake in annual revenues of ₹1,000 crore post the mandate. Uno Minda generates ₹350-400 crore from airbags at present. The company has a significant presence in A and B segments of passenger vehicles — where transition to six airbags has not taken place — and that is what the auto components maker wants to tap.
With multi-fold increase in demand imminent, airbag makers will pull out all stops to corner market share in the Indian automobile market, which recently pipped Japan to become the third-largest in the world.
Leave a Comment
Your email address will not be published. Required field are marked*