Surrounded by waterfalls and Amazon forest-like greenery, the Venkateswara Temple, also known as the Balaji Temple of Tirupati, in the southeastern part of Andhra Pradesh draws millions of visitors every year. The sprawling seven hills are held sacred by devotees and revered as the abode of Lord Venkateswara.
In this temple town, just a few kilometers away are not one, but two factories run by Amara Raja Batteries Ltd., India’s second-largest industrial and automotive battery maker.
Amara Raja, with its brand Amaron, is one of the two companies that form a duopoly in the subcontinent when it comes to batteries for trucks, buses, cars and bikes. Exide Industries is the second, and together they control around 80% of the domestic batteries market.
Yet, despite the dominant advantage, companies such as Amara Raja are finding themselves in the middle of an existential challenge. The era of electric vehicles is right here. While market penetration and sales figures for next-generation vehicles are still low, the reality is that to be future-ready manufacturers and OEMs have to make the big-ticket capex right now.
At one level, traditional technology, the lead acid battery business, cannot be abandoned since it is the cash cow, and continues to grow. Amara Raja, for instance, reported a net profit of ₹512 crore on net revenues of ₹8,697 crore in FY22. Despite the rise of EVs, players have to continue making investments in this business, enhancing capacity, and foraying overseas. At the same time, they have to also start making moves in new chemistries, new-age vehicles, and technologies such as hydrogen and sodium.
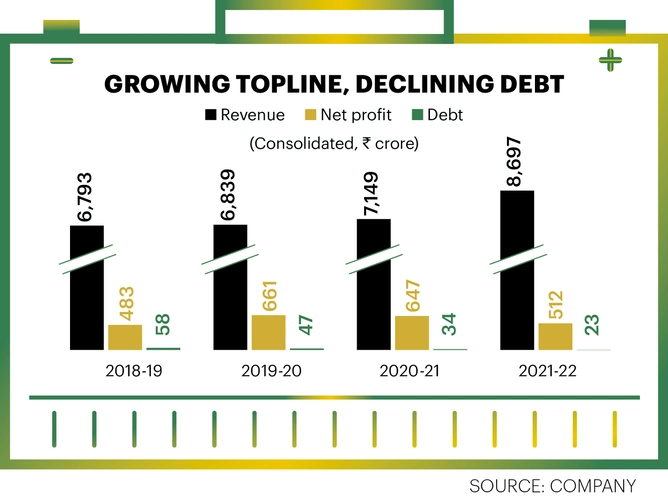
“Lead acid battery technology has been around for 100 years, it may be around for another 100 years, and probably longer than lithium-ion, because lithium-ion is going to change to the next flavour of the day, in the next decade or two, if not sooner,” says Jay Galla, co-founder and chairman, Amara Raja.
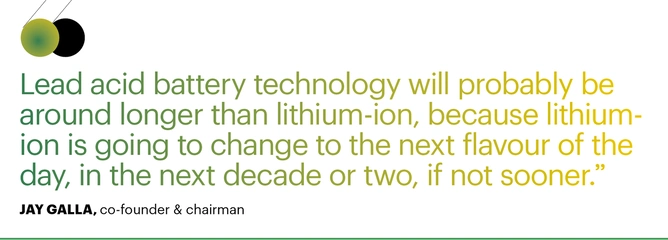
Galla believes lead acid has certain usage and will continue to be relevant as long as it is cost effective. It may not be in demand like lithium-ion due to the latter’s sheer volume, but will retain its hold on niche applications, regardless of the changes in the EV space.
In fact, there are industries that mostly deploy lead acid batteries, such as telecom towers. NexGen single mast towers have begun deploying lithium-ion batteries.
“Tomorrow, as we go into 5G, they will become much smaller sites, powered by lithium-ions. But in the case of EVs, lead acid will continue to power low voltage systems,” adds Galla.
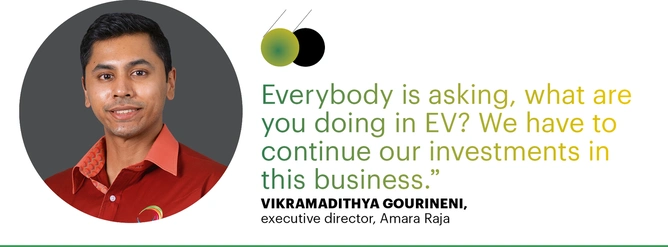
“Traditional batteries remain the cash cow,” says executive director Vikramadithya Gourineni. “They continue to do well and grow. Everybody is asking, what are you doing in EV? We have to continue our investments in this business, including enhancing capacity, and even going global.”
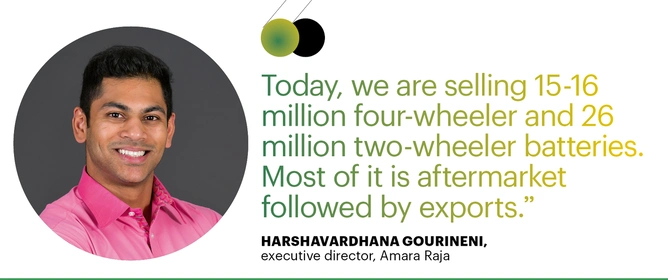
His brother Harshavardhana Gourineni, also an executive director, agrees. “Today, we are selling 15-16 million four-wheeler and 26 million two-wheeler batteries. Most of it is aftermarket followed by exports. And then there are the OEM channels.”
So what does a company do when it is at such a cross-road?
A couple of months ago, Amara Raja unveiled how it sees the future. The company, which is both the largest taxpayer as well as the largest private sector employer in its region, signed an MoU with the Government of Telangana to set up research and manufacturing facilities for lithium-ion battery making in Mahbubnagar district. Over the next decade, it will invest around ₹9,500 crore in capex and new technology. Dubbed the Amara Raja Giga Corridor, initial facilities would include a first-of-its-kind advanced energy research and innovation centre in Hyderabad, the Amara Raja E-hub. The facility will have advanced laboratories and testing infrastructure for material research, prototyping, product life cycle analysis and proof of concept demonstration. The lithium-ion battery Giga factory will have an ultimate capacity of 16GWH and a battery pack assembly unit up to 5GWH.
Others such as Maruti Suzuki have also jumped on the bandwagon. Maruti Suzuki, for example, is setting up the TDS lithium-ion battery plant, a joint venture between Toshiba, Denso and Suzuki, in Hansalpur, Gujarat.
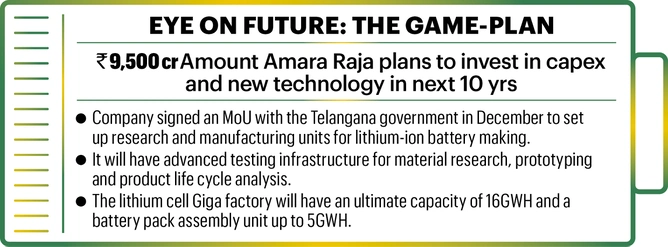
BATTERIES AND BEYOND
In November, 2022, Amara Raja incorporated subsidiary Amara Raja Advanced Cell Technologies. The company has been working on Li-ion cell chemistries specifically for the Indian subcontinent, and supplies lithium battery packs and chargers to some two- and three-wheeler OEMs.
The move is both strategic and timely, says Suraj Ghosh, director, mobility, S&P Global. “It is an important step signaling the company’s strategic direction and how the future will play out in both mobility and energy storage. At the same time, the research and development effort it is pursuing for cells is an indicator of its plans of exploring the entire value chain for EVs. But raw materials, processing and ongoing partnerships with mining companies where rare earth minerals are available will also need strategic thinking and participation.”
Ghosh also thinks that while China has a stronghold in cost and scale for battery makers, India can compete as an alternative. “In the know-how, packaging and processing of cells, India can create a niche for itself.”
Scientifically, every EV requires a low voltage system to power electronics and other gadgetry, which doesn’t come from the main battery. “So even in an EV, we still use a lead acid battery, sometimes a larger one than in a normal, conventional car,” says Galla.
He believes even if all cars were to switch to EVs overnight, companies such as Amara Raja would not be impacted suddenly, since there would be a need for other options for back-up power. However, he’s aware that moving on from lead acid is the evolution that needs a closer watch than the penetration of EVs. “We need to see the capability and requirements of the battery for low voltage systems and cars, and how that is growing,” says Galla. So far the number of EVs registered in India is below a mere 5%, according to the Center for Science and Environment, but there is ample room for growth.
So, how stable is Amara Raja’s present position in the market?
“In India, we have around 35% share in the aftermarket,” says Galla. But that doesn’t make him complacent. “At some point, a third player can start pushing in, because there’s a conceptual limit on how big you can go in a single market. We can continue to grow with the market and maybe slightly ahead of the market. That’s why we are looking at exports as the new channel of growth.”
The risk of foreign competition could come from China-based Contemporary Amperex Technology Co. Ltd. (CATL), and five-six others that are on track to be global players.
So, how do battery makers read the tea leaves for their business?
“Data shows that penetration of four-wheelers in Indian households is about 5%. But for two-wheelers, it is at about 80%,” says Galla. Even if the number is something close by, India will reach a peak shortly in terms of market size for two-wheelers. “As more people switch to other forms of vehicles, it may decline over time also, so we may not see huge growth rates in two-wheelers as in the past,” adds Galla.
There’s also a peculiar duality that plays out. Harshavardhana says existing tech for battery making hasn’t changed much over the years. All batteries are made of lead which gets converted into lead oxide after it goes into a mill and comes out as powder. Lead is again used as a raw material and melted down into slurry, which then goes into making battery plates. There is a mould in which liquid molten lead is poured in. Once these plates are processed and punched under high compression so that they are a few millimetres thick, the plates are dried and taken to be assembled within a plastic container. These plates are both positive and negative, and are assembled into six prismatic cells, with alternating positive and negative components put in a pouch, and then fitted into battery containers. The containers are then filled with sulphuric acid and the process undergoes ‘formation’, where through charge-discharge the battery gets its original charge. Once the process is complete, the batteries are sealed, labelled and shipped.
And is the race to be No. 1 vital for the group, given that Exide is larger? “We have a much larger stake in the passenger vehicle segment, but have limited our volume since there’s little profit in the segment. If our only goal is to be larger, we would have to sacrifice things, which we don’t want,” says Galla. Getting larger than Exide won’t necessarily make them the largest battery manufacturer going forward, because with the EV revolution, both may get dwarfed, unless they set their sights differently going forward,” he adds.
There’s also a technical facet to the trade that is dependent on commodities and supply chain pressures. Raw materials such as cobalt, which are in short supply due to price fluctuations or conflict, have a bearing on the business, says Vikramadithya. “If we can migrate from cobalt in our chemistry, it can make a difference,” he adds. “Tesla, for instance, uses nickel-rich chemistry. But nickel is extremely price sensitive and may actually end up being a bottleneck in the future. So they are now trying a manganese-rich chemistry to reduce the requirement of nickel. Then we also have alternate lithium chemistries with iron being the most prominent. It was popularised by Chinese players, but most geographies are now embracing it. The funniest thing is that lithium, despite having batteries named after it, is not a very big part and will not be a bottleneck.”
At the end of the day, it’s a lithium battery, whether it’s made in India or China, but if a homegrown player can modify its chemistry to suit the Indian requirement, and not just performance, but even what can be sourced easily, it will make a winning difference to output and even global supply. The tricky part about the EV battery business is that it is constantly changing. “There is no singular technology that will be the mainstay for the next few decades, so battery makers have to be flexible... It could be an opportunity or a risk,” says S&P Global’s Ghosh.
All of these bring Amara Raja back to the double-edged sword that comes with transition to the next level of technology for EVs.
The EV world order, says Vikramadithya, is very different pre- and post-Tesla. “Earlier, you saw East Asian countries such as Japan and Korea leading the charge with hybrid vehicles. Even now, many of those vehicles, such as the Toyota Prius which is some 20 years old, and the Nissan Leaf have competitive carbon footprints compared with most EVs in the market. EVs will only come into their own when their charging is done with greener energy and there is higher utilisation of the vehicle. Whether the credit really goes to Tesla or not, the fact is, most OEMs were quite slow on the trigger with electric until they came to prominence,” he adds.
On ground OEMs are experimenting with electric portfolios, but they don’t want to close down factories since they want to play both ways. Suppliers, therefore, will have to oblige. “So, we have to be ready to meet customers’ demands and requirements in the form of electric vehicles. But if demand for traditional vehicles continues, which will, at least for the next 10-20 years, we have to continue to cater to that demand,” says Vikramadithya. In other words, charging firms would need to have one foot in the present and another taking a leap firmly into the future.